Kinetic Recovery Rope info/use
ASR has been making Kinetic Recovery Ropes since 2011. Kinetic Recovery Ropes (also known as a snatch ropes or yanker ropes) are designed to stretch, to smoothly transfer the kinetic energy of a recovering vehicle to a vehicle that is stuck. The ability of a Kinetic Recovery Rope to stretch is what makes it unique and what sets it apart from a non-elastic tow rope or tow strap. ASR Offroad's Kinetic Recovery Ropes are designed and built for the express purpose of stretching under load, to provide a smooth and powerful pull. Some key features that set our Kinetic Recovery Ropes apart:
- 100% MILSPEC Double Braid Nylon.
- No solution dyes (solution dyed Nylon can have an approx 10% lower MTS).
- Professionally spliced in the US.
- Abrasion protection in the eyes and on the rope body.
- Optional fiber-lock coating of the exterior in a custom color.
- Up To 20% Elongation when used properly while under load (30% stretch at Breaking Strength).
Benefits of Using ASR's Kinetic Recovery Ropes over other recovery/tow equipment:
- More durable and therefore less susceptible to damage from normal wear and tear.
- Decreased shock loads on Recovery Mounting Points.
- Able to transfer significant kinetic energy, even when the "assist vehicle" is much smaller than the "stuck vehicle".
- Superior performance even in very low traction situations.
- Lightweight and portable.
How to Correctly Use Your Kinetic Recovery Rope
Kinetic Recovery Rope Specifications & Selection
Many environmental factors such as slope, type and consistency of terrain the vehilce is mired in, and mire depth all play a role in determining the force that will be required to recover the stuck vehicle - the Safe-Xtract Vehicle Recovery App (available for both Android and iOS devices) does an excellent job of calculating a total resistance based on all these factors and more. In extreme environmental conditions, it may be desirable to increase rope diameter by one level. We do not recommend decreasing the diameter for lighter environmental conditions.
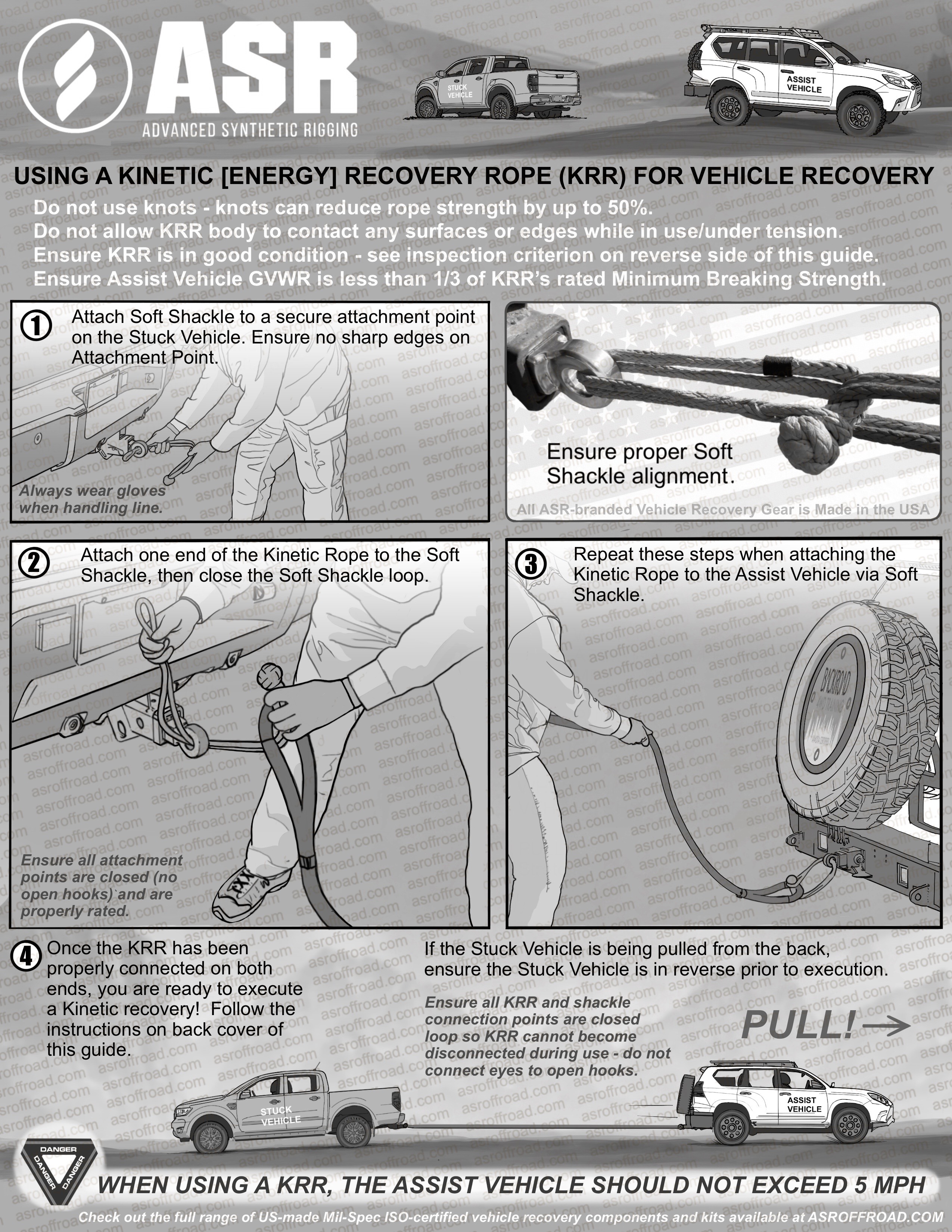
WARNING: ROPE FAILURE CAN CAUSE SERIOUS INJURY OR DEATH. When using a Kinetic Recovery Rope, the Assist Vehicle should not exceed 5 mph. If the Assist Vehicle pulls the rope tight at too high a speed, the resulting ‘shock loading’ can damage or even break the attachment point, vehicle frame or KRR. The user is responsible to determine the suitability of a rope for specific applications.